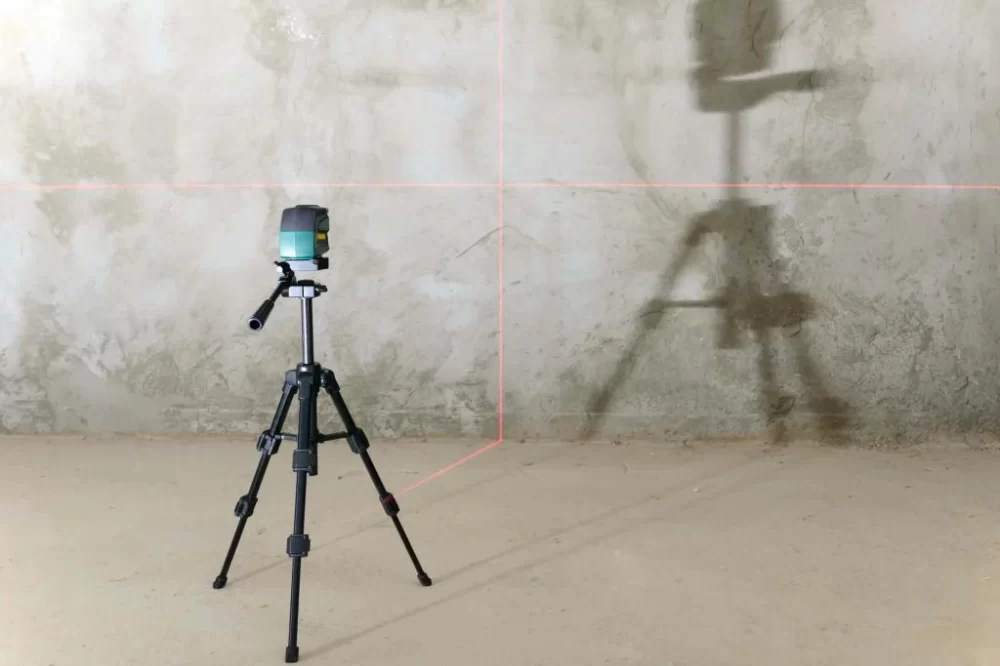
Understanding Laser Level Calibration
As a DIY enthusiast or professional contractor, you know that accurate measurements are crucial for any project. Whether you're installing shelves, laying flooring, or constructing a building, a laser level can make your job easier and more precise. But just like any tool, it requires calibration to ensure it works properly. In this article, I will walk you through the steps on how to calibrate a laser level and why it's so important.
Why Calibrating Your Laser Level is Essential
Calibration is the process of adjusting your laser level to ensure it delivers accurate and precise measurements. If your laser level isn’t calibrated correctly, your measurements could be off, leading to crooked lines, uneven surfaces, and costly mistakes. But don’t worry—calibrating your laser level is simple and can save you time, effort, and money. Here’s why calibration is essential:
- Accuracy: Calibration ensures that your laser level projects straight lines and measurements, which is crucial for any project.
- Efficiency: A well-calibrated laser level reduces the chances of errors, meaning fewer adjustments and rework during the project.
- Longevity: Regular calibration helps maintain the tool’s performance and extends its lifespan.
Tools You’ll Need for Laser Level Calibration
Before you begin the calibration process, it’s important to gather the right tools. Here’s a list of essential items that will make the job easier:
- Laser level
- Flat, level surface (preferably a floor or a large table)
- A tape measure
- A measuring square or a level ruler
- A target or wall to project the laser onto
- A tripod (if your laser level requires one)
Step-by-Step Guide to Calibrate a Laser Level
Now that we’ve discussed why calibration is so important and what tools you’ll need, let’s jump into the actual process. Follow these simple steps to calibrate your laser level and ensure accuracy:
Step 1: Place the Laser Level on a Stable Surface
Start by positioning your laser level on a stable, flat surface. This could be a floor, a table, or even a tripod, depending on your laser level's design. Make sure the surface is level—this is crucial, as any tilt can throw off the calibration.
Step 2: Power On the Laser Level
Once your laser level is securely positioned, power it on. Most laser levels will automatically project a line or dot, but check your specific model for instructions. For the most accurate results, make sure the laser is in the calibration mode (refer to your manual if necessary).
Step 3: Adjust the Horizontal or Vertical Alignment
Now, you’ll need to adjust the alignment of the laser level. Depending on the model you have, there may be screws or dials you can adjust. Align the laser’s projected line or dot with a reference point on a nearby wall or surface. Use a measuring square or a level ruler to ensure that the line is perfectly horizontal or vertical, depending on what you're calibrating.
Step 4: Measure the Accuracy
Take your tape measure and measure the distance between the laser line and the surface at a few different points. Ideally, the measurements should be the same along the entire length of the laser’s projection. If the measurements vary, this indicates that the laser level is out of calibration.
Step 5: Make Fine Adjustments
If your measurements aren’t consistent, make small adjustments to the calibration screws or knobs. Adjust the laser level until it projects a straight and accurate line. This process may require some trial and error, but it’s essential for getting the best results.
Step 6: Test the Calibration
Once you believe the laser level is calibrated, test it by using it on an actual project. Set the level on a known surface and check its accuracy against a known measurement. If everything checks out, you’re good to go!
Common Calibration Mistakes to Avoid
As I was calibrating my laser level for the first time, I made a few common mistakes that caused me frustration. Here are some pitfalls to avoid:
- Not using a level surface: This is the most common mistake people make. A tilted surface can throw off the entire calibration process.
- Ignoring the manufacturer’s instructions: Each laser level is slightly different. Always refer to your manual for specific calibration steps.
- Not testing before use: After calibrating, always test your laser level on a real project to ensure accuracy.
How Often Should You Calibrate Your Laser Level?
Calibrating your laser level regularly is key to maintaining accuracy. As a general rule, you should calibrate your laser level:
- Before starting a new project
- If you notice any misalignment or measurement issues
- After dropping or bumping the laser level
- Every few months for general maintenance
Final Thoughts
Laser levels are indispensable tools for ensuring precision in your projects. Calibration might seem complicated, but with the right tools and a little practice, it’s a simple task that can greatly improve your results. If you're ever in doubt, don’t hesitate to refer to the manufacturer's guide or seek professional help. Keep your laser level calibrated, and you’ll enjoy accurate, hassle-free measurements every time!